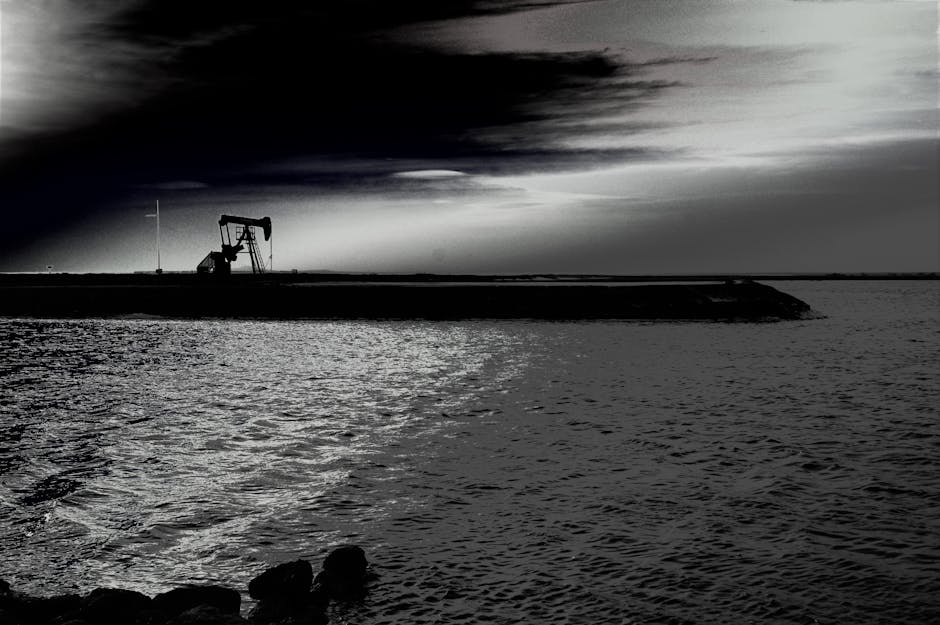
Explore oil rig welding: roles, skills, safety, and earnings. Understand the challenges and enhance productivity offshore.
Oil rig welding is a crucial trade that keeps offshore oil platforms operating smoothly and safely. If you're working on a construction site or managing a crew, you know the importance of having reliable tools that can handle tough jobs. Oil rig welding involves maintaining and repairing various parts of an offshore facility, including small maintenance tasks and dealing with complex corrosion-resistant alloys. This work is vital in preventing downtime and ensuring the productivity of oil rigs.
I'm None, and my journey with oil rig welding has spanned over 20 years, taking me across various challenging environments worldwide. From working with diverse welding techniques such as TIG and MIG to tackling demanding welding projects, I've developed a deep understanding of this trade. Oil rig welding is more than just a job; it's about delivering quality and precision, always with safety in mind.
Common oil rig welding vocab:
Oil rig welding is a specialized trade focused on maintaining and repairing offshore platforms. These platforms are large structures in the ocean, used for drilling and extracting oil and gas. Welding on these rigs is essential for keeping everything safe and operational.
A rig welder is a key player on an offshore platform. They handle all welding tasks, from small maintenance jobs to more complex projects involving corrosion-resistant alloys. Usually, there are only one or two welders on a rig, so they must be versatile and skilled. Their work ensures that the platform remains structurally sound and capable of withstanding harsh ocean conditions.
Working on an oil rig requires specialized welding equipment designed to handle the unique challenges of the offshore environment. This includes:
Offshore platforms are like small floating cities. They have living quarters, machinery, and everything needed to extract oil and gas. Welding on these platforms is not just about fixing things; it's about ensuring the entire operation runs smoothly. Welders must adapt to the ever-present motion of the sea and the potential for extreme weather conditions.
Oil rig welding is a demanding but rewarding career. It requires a combination of technical skills, problem-solving abilities, and a strong commitment to safety. Whether repairing a small pipe or reinforcing a large structure, welders play a vital role in the success of offshore oil operations.
Welding on oil rigs involves a variety of techniques, each suited to specific tasks and materials. Two of the most common methods are Gas Tungsten Arc Welding (GTAW) and Shielded Metal Arc Welding (SMAW). Let's explore what makes these techniques essential for oil rig welding.
GTAW, also known as TIG welding, is a precise welding method often used for the root runs of single-sided welds in piping. It's especially vital when working with Corrosion Resistant Alloys (CRAs) and thin materials. These materials are frequently found on oil rigs due to their durability in harsh, salty environments.
SMAW is another staple in the oil rig welder's toolkit, often used for fill and cap passes on piping and welding structural steel components. It's versatile and reliable, making it a go-to method for many welding tasks on oil rigs.
Oil rigs are built with various materials, each chosen for specific properties required in the offshore environment:
The choice between GTAW and SMAW, and the materials used, depends on the specific demands of the job. Each technique and material has its strengths, custom to withstand the unique challenges of the offshore environment. By mastering these methods, oil rig welders ensure the safety and efficiency of oil extraction operations.
In oil rig welding, understanding the right techniques and materials is crucial. It ensures that welders can handle the diverse challenges they face on offshore platforms. Up next, we'll explore the skills and qualifications needed to excel in this demanding field.
To excel in oil rig welding, a combination of education, hands-on training, and certifications is crucial. Let's break down what you need to get started and advance in this challenging yet rewarding field.
A high school diploma or an equivalent certification like a GED is the first step. This educational foundation is vital as it ensures you have basic skills in math, reading, and writing, which are essential for interpreting blueprints and technical documents.
After high school, attending a trade school is a common path. These programs offer a mix of classroom learning and practical experience. You'll learn essential welding techniques, such as Flux Cored Arc Welding (FCAW) and Gas Metal Arc Welding (GMAW). Trade schools also teach you how to:
Completing a trade school program prepares you for entry-level positions, such as a welding apprentice or industrial welder.
Certifications are critical in the welding industry, especially for specialized roles like oil rig welding. They demonstrate your skill level and commitment to safety. Some key certifications include:
Certifications not only improve your skills but also increase your job prospects and potential earnings.
While education and certifications are important, gaining real-world experience is invaluable. Entry-level jobs and apprenticeships provide on-the-job training, allowing you to work with various materials and stay updated on industry innovations.
In the field of oil rig welding, having the right mix of education, training, and certifications is key to advancing your career. With these qualifications, you'll be well-equipped to tackle the challenges of welding in the offshore environment.
Up next, we'll dig into the specialized roles within oil rig welding, from pipeline welders to hardbander welders.
In oil rig welding, each role is unique, requiring specific skills and expertise. Let's explore the specialized roles that keep offshore platforms running smoothly.
Pipeline welders are crucial for maintaining the integrity of pipelines that transport oil and gas. They specialize in Gas Tungsten Arc Welding (GTAW) and Shielded Metal Arc Welding (SMAW), techniques essential for creating strong, leak-proof joints. These welders must be adept at working with various materials like carbon steel and stainless steel, ensuring that pipelines withstand harsh ocean conditions.
Ironworkers on oil rigs focus on constructing and maintaining the rig's structural framework. They work with large steel beams and girders, using SMAW techniques to ensure stability and safety. Ironworkers must be able to interpret blueprints and work at great heights, often in challenging weather conditions.
Fitters play a vital role in assembling and installing piping systems on oil rigs. They measure, cut, and fit pipes to exact specifications, working closely with pipeline welders to ensure seamless connections. Fitters must have a strong understanding of technical drawings and be capable of performing precise calculations to maintain system integrity.
Spot welders specialize in making quick, localized welds that join thin pieces of metal. This role is essential for tasks like repairing small components or reinforcing structures without affecting surrounding areas. Spot welders must be precise and efficient, often working in confined spaces where accuracy is critical.
Hardbander welders focus on applying protective coatings to drill pipe joints, known as hardbanding. This process extends the life of drilling equipment by reducing wear and tear. Hardbander welders must be skilled in applying these coatings evenly and consistently, ensuring that the equipment can withstand the rigors of drilling operations.
Each of these specialized roles requires a unique set of skills and expertise, contributing to the overall success and safety of oil rig welding operations. We'll explore the challenges and safety protocols that define this demanding field.
Oil rig welding is not just about joining metal; it's about doing so in one of the most hazardous environments on Earth. Welders on offshore platforms face unique challenges that demand strict adherence to safety protocols.
Oil rigs are inherently dangerous places. They float on open water, often far from shore, and are exposed to extreme weather conditions. These platforms are busy with heavy machinery, high-pressure systems, and flammable materials. The risk of fire or explosion is ever-present, especially when welding is involved.
Safety is the top priority in oil rig welding. Rig welders must follow strict safety protocols to prevent accidents. This includes obtaining the correct permits and following "permit to work" systems that ensure all safety measures are in place before welding begins. Welders must wear flame-resistant clothing and use specialized equipment to protect against sparks and heat.
Training is essential. Every welder must complete offshore survival training and helicopter underwater escape training (HUET). These courses prepare them for emergencies, such as evacuating a rig by helicopter. Additionally, welders must pass rigorous medical exams to ensure they can handle the physical demands of the job.
One of the unique safety measures on oil rigs is the use of pressurized habitats. These are specially constructed areas where welding can be done safely. The habitat is pressurized to keep flammable gases out, reducing the risk of explosions. Inside, welders can work without the fear of igniting the volatile atmosphere outside.
These habitats are typically made from plasticized fabric or plywood, supported by scaffolding. They create a controlled environment where sparks and heat are contained. This setup is crucial for maintaining safety while allowing critical welding tasks to proceed.
Understanding and respecting these challenges and safety protocols is vital for anyone involved in oil rig welding. As we dig deeper into this field, we'll address common questions about the life and work of an oil rig welder.
Oil rig welders are well-compensated for their specialized skills and the challenging environments they work in. Salaries can vary significantly based on location and experience. In Norway, welders earn about $30 per hour, which is higher than their counterparts in countries like the UK and South Korea. In the United States, the hourly rate can be even higher, reflecting the demand for skilled welders in the oil and gas sector.
Top earners in countries like Australia can make an annual salary of around $140,000, according to the Global Energy Talent Index Report. North American oil rig welders follow closely, with average salaries reaching $112,000 per year.
On oil rigs, welders primarily use Gas Tungsten Arc Welding (GTAW) and Shielded Metal Arc Welding (SMAW). These techniques are essential for the variety of materials encountered in the offshore environment.
GTAW, often used for the root runs of single-sided welds, is crucial when dealing with Corrosion Resistant Alloys (CRAs) or thin materials. It provides precise control, which is necessary for high-quality welds in critical applications.
SMAW is commonly used for fill and cap passes on piping and structural steel components. This method is versatile and effective for robust, durable welds, making it a staple technique in oil rig operations.
Becoming an oil rig welder requires dedication and a specific set of skills and qualifications. The journey typically begins with earning a high school diploma or GED. From there, aspiring welders should complete a vocational program in welding, which covers essential techniques such as welding, brazing, and soldering.
Hands-on training is crucial. Apprenticeships or entry-level positions provide the experience needed to work on oil rigs. During this time, welders learn to work with various materials and stay updated on industry innovations.
Certifications in offshore survival and helicopter underwater escape training (HUET) are mandatory. These prepare welders for the unique challenges of the offshore environment, ensuring they can handle emergencies and the physical demands of the job.
While the path to becoming an oil rig welder can be demanding, the rewards—both financial and personal—make it a worthwhile pursuit for those committed to mastering the craft.
Oil rig welding is a specialized field that plays a critical role in the energy industry. The work is demanding, requiring a unique blend of skills, certifications, and safety awareness. However, the rewards are significant, both in terms of compensation and the sense of accomplishment that comes from keeping vital infrastructure operational and safe.
At Tentacle Tools, we understand the importance of having the right equipment to improve job performance and productivity. Our products are designed and tested by experts to meet the rigorous demands of welding in challenging environments like oil rigs. We offer a range of tools that are not only reliable but also improve efficiency, helping welders perform their tasks with precision and safety.
Explore our catalog to find the tools that can lift your welding projects. Whether you're a seasoned professional or just starting out, our products are here to support you every step of the way.
In the changing landscape of oil rig welding, staying equipped with the best tools and knowledge is crucial. As the industry grows and changes, so too does the need for skilled welders who can adapt and excel. With the right training, certifications, and equipment, the opportunities in this field are vast and rewarding.
Explore insights, tips, and trends in tech and productivity!